
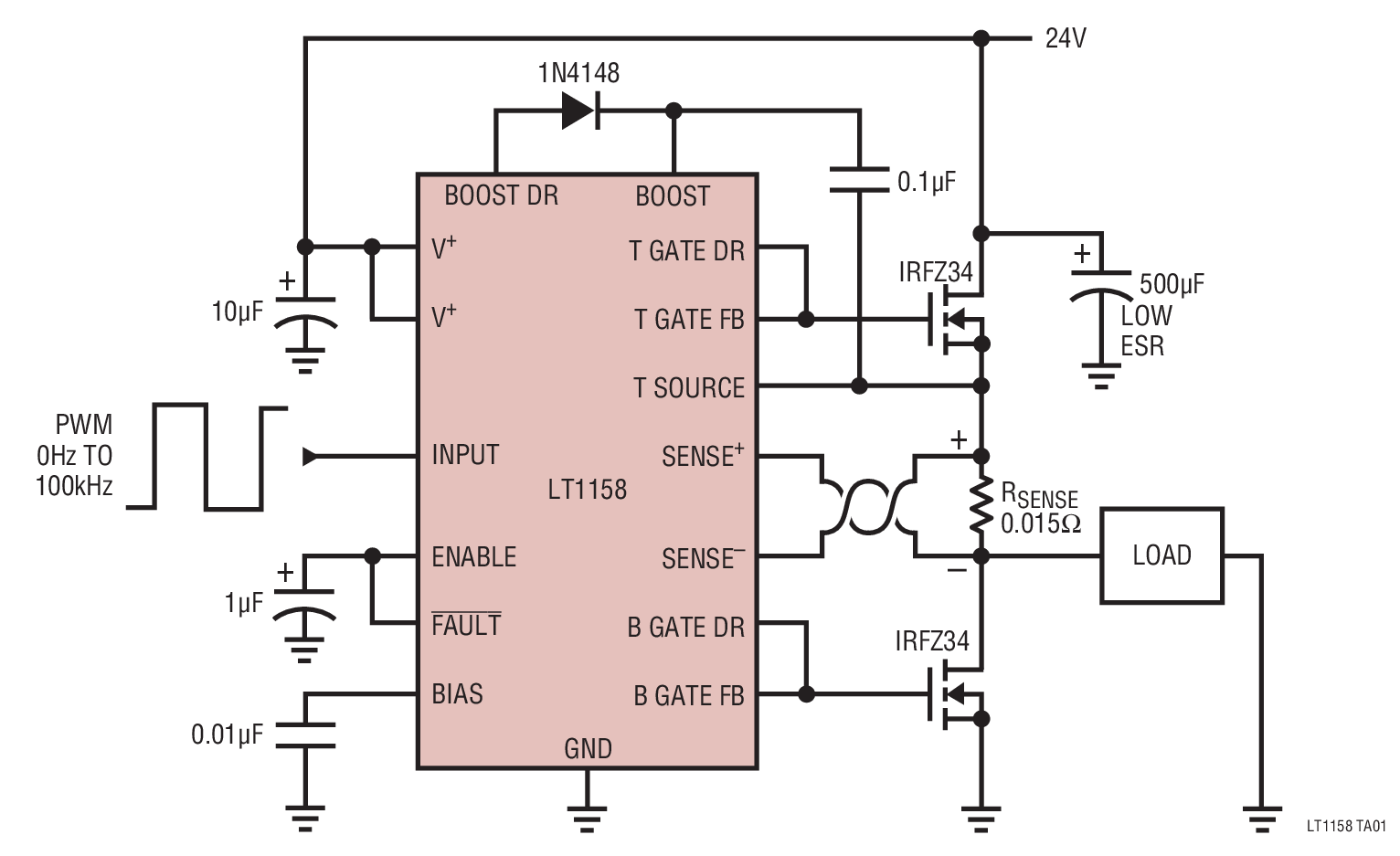
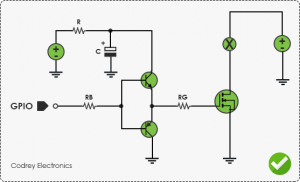
Light duty, medium duty, and heavy duty are terms to differentiate encoders by indicating how much load can be applied to the shaft. Regardless of the sensing technology employed, the encoder’s electronics sense movement and translate that motion into industry-standard electrical signals. These encoders are as rugged as magnetic encoders, but also do not achieve the high resolution and accuracy of optical encoders. They are often used in environments with excessive dirt, steam, vibrations and other environmental factors that could interfere with optical encoder performance.Ĭapacitive encoders are relative newcomers to industrial automation. Magnetic encoders are more rugged than optical encoders, but have less resolution and accuracy. This optical rotary encoder is often used in industrial automation applications to sense rotary motion. When specifying an optical encoder, it’s important that the encoder has extra protection built in to prevent contamination from dust, vibration and other conditions common to industrial environments. Optical encoders are the most accurate of the standard styles of encoders, and the most commonly used in industrial automation applications (Figure 1).

The position information can be determined using one of three technologies: optical, magnetic or capacitive. Regardless of type, all encoders provide a type of orientation that’s used as a reference point for position control.Īn encoder (for industrial controls) is a special sensor that captures position information and relays that data to other devices. They provide information required for the precise control of a variety of applications, such as positioning a rotary table, pick and place, machine assembly, packaging, robotics and more.

Updated June 2016 by Lisa Eitel || by Joe Kimbrell, Product manager, Drives, Motors and Motion, AutomationDirectĮncoders are used to determine the position, velocity and direction of motor shaft speed and other mechanical motion.
